Aluminum Coil
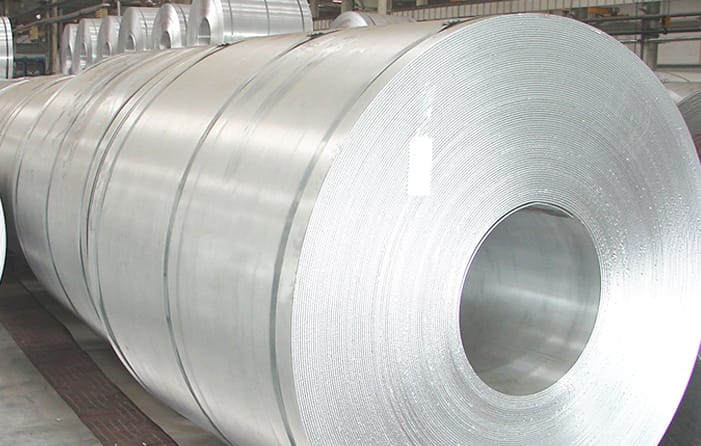
Aluminum Coil
Aluminum coil is a kind of metal plate, melted by aluminum ingots, plus different alloys, through casting or rolling or hot rolling, cold rolling, annealing, transverse shear and other processes into aluminum coil, aluminum coil has low density, light weight.
Aluminum can be recycled an infinite number of times, meaning it is an environmentally friendly metal. JUHE produces high-quality aluminum in many shapes, sizes, and grades, so you’re always guaranteed to find what you need from us.
Available Size Range
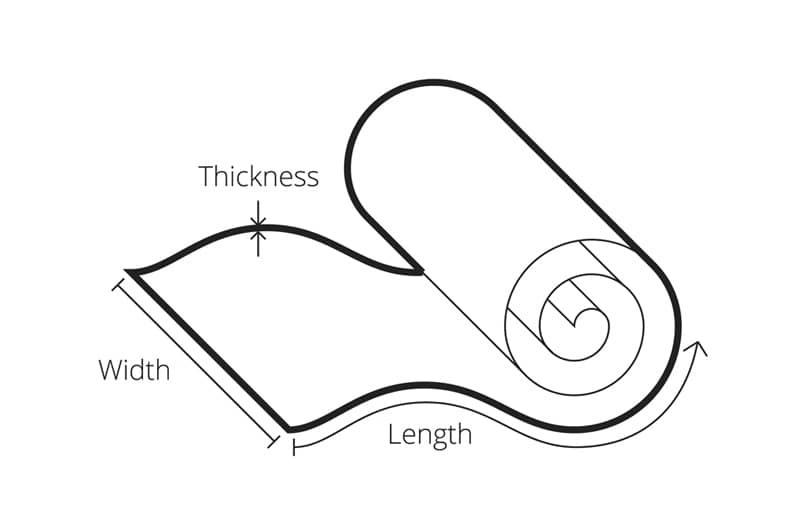
0.2-200mm or customize
100-2600mm Or customize
2000mm,2440mm,6000mm,or as required.
Product Specification
Product Name | Aluminum coil |
---|---|
Standard | GB/T3190-2008, GB/T3880-2006, ASTM B209, JIS H4000-2006, etc |
Sample | Provide free samples |
Material | 1050,1060,2A14,3003,3103,4032,5454,5754,5056,5082,5086,6061,6060,6082,7075,7475 etc. |
Surface | Bright,polished,hair line,brush,sand blast,checkered,embossed,etching.etc |
Remark | Specific requirement of alloy grade,temper or specification can be discussed at your request |
Technology | Hot Rolled ( DC ), Cold Rolling ( CC ), cast |
Temper | O/H111 H112 H116/H321 H12/H22/H32 H14/H24/H34/H16/H26/H36 H18/H28/H38 H114/H194, etc. |
Package | Standard export package,such as wooden box or as required. |
Satisfy Your Needs | We can customize product specifications, sizes and shapes according to your requirements. |
Application | 1)Further making utensil 2)Solar reflective film 3)The appearance of the building 4)lnterior decorating; ceilings,walls,etc 5)Furniture cabinets 6)Elevator decoraction 7)Signs, nameplate,bags making 8)Decorated inside and outside the car 9)Household appliances:refrigerators, microwave ovensaudio equipment,etc |
Producing Process
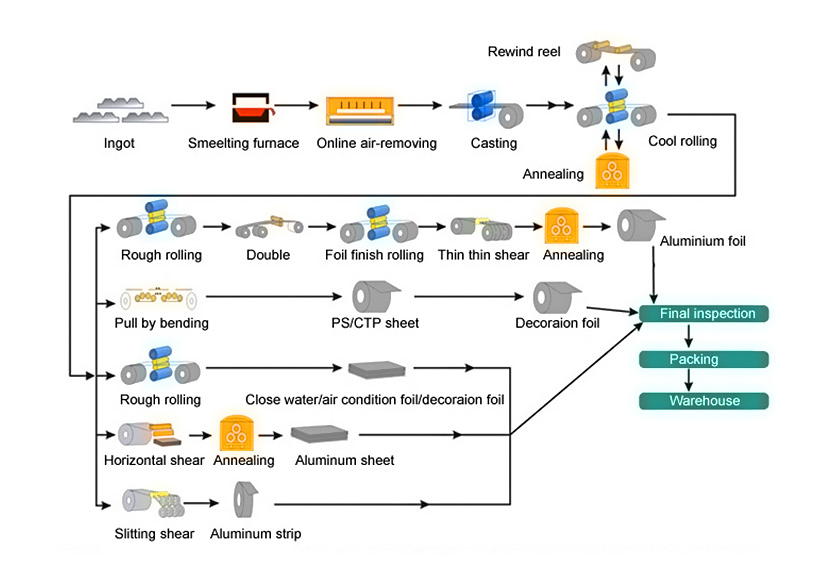
Aluminum Ingot/Master Alloys — Melting Furnace — Holding Furnace — Slab — Hot Rolling — Cold Rolling — Slitting machine (vertical cutting to narrow width) — Annealing Furnace (unwinding) — Final Inspection — Packing — Delivery
Chemical Composition(For Reference)
Aluminium alloy grade including 1xxx, 2xxx, 3xxx, 4xxx, 5xxx, 6xxx, 7xxx, 8xxx. But the most common is 1050, 3003, 6061, and 5251 aluminum coil. Common widths of the aluminum coil are 800mm,1000mm, 1250mm,1450mm, and 1500mm.
Alloy Series | Typical Alloy | Introduction |
---|---|---|
1000 Series | 1050 1060 1070 1100 | Industrial Pure Aluminum. Of all series, the 1000 series belongs to the series with the largest aluminum content. The purity can reach over 99.00%. |
2000 Series | 2024(2A12), LY12, LY11, 2A11, 2A14(LD10), 2017, 2A17 | Aluminum-copper Alloys. 2000 series is characterized by high hardness, in which the content of copper is the highest, about 3-5%. |
3000 Series | 3A21、3003、3103、3004、3005、3105 | Aluminum-manganese Alloys. 3000 series aluminum sheet is mainly composed of manganese. The manganese content ranges from 1.0% to 1.5%. It is a series with a better rust-proof function. |
4000 Series | 4A03、4A11、4A13、4A17、4004、4032、4043、4043A、4047、4047A | Al-Si Alloys. Usually, the silicon content is between 4.5 and 6.0%. It belongs to building materials, mechanical parts, forging materials, welding materials, low melting points, and good corrosion resistance. |
5000 Series | 5052, 5083, 5754, 5005, 5086,5182 | Al-Mg Alloys. 5000 series aluminum alloy belongs to the more commonly used alloy aluminum series, the main element is magnesium, and the magnesium content is between 3-5%. The main characteristics are low density, high tensile strength, and high elongation. |
6000 Series | 6063、6061、6060、6351、6070、6181、6082、6A02 | Aluminum Magnesium Silicon Alloys. The representative 6061 mainly contains magnesium and silicon, so it concentrates on the advantages of the 4000 series and 5000 Series. 6061 is a cold-treated aluminum forging product, which is suitable for applications requiring high corrosion resistance and oxidation resistance. |
7000 Series | 7075、7A04、7A09、7A52、7A05 | Aluminum, Zinc, Magnesium, and Copper Alloys. The representative 7075 mainly contains zinc. It is a heat-treatable alloy, belongs to super-hard aluminum alloy, and has good wear resistance. 7075 aluminum plate is stress-relieved and will not deform or warp after processing. |
Transportation
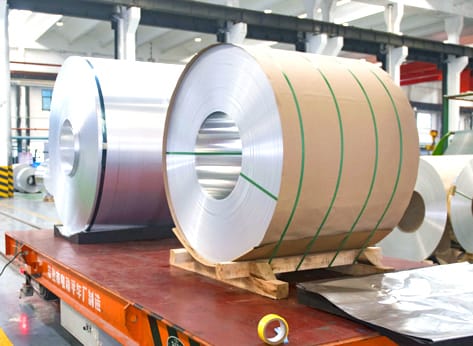
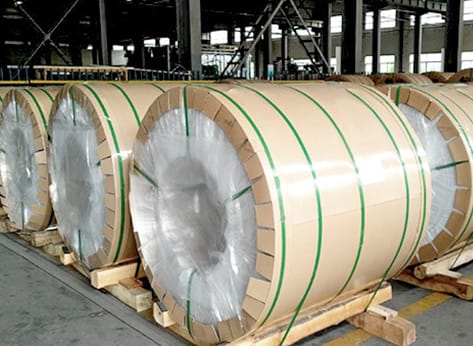
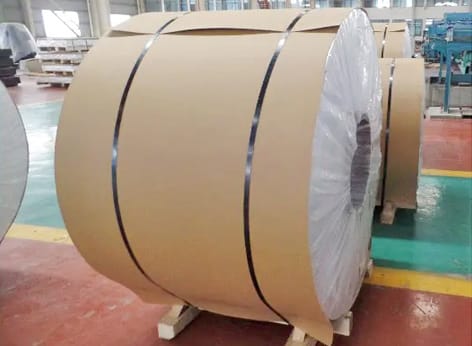
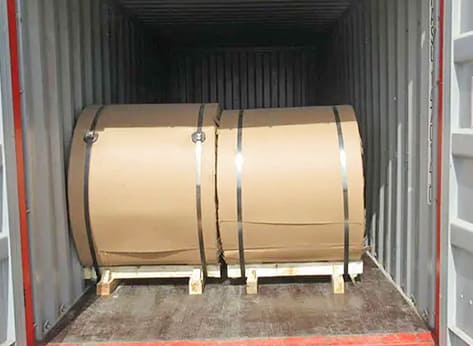
Product Inspection
Here are some key factors to consider when inspecting aluminum coils:
- Size: Check the size of the coil against the specifications provided by the manufacturer. Make sure they are the correct thickness, width and length.
- Surface quality: Check the coil surface for scratches, dents or other defects. The surface should be smooth without any visible damage.
- Color consistency: the color of the coil should be consistent throughout the coil. Any change in color could indicate a problem with the production process.
- Coating thickness: If the coil has coating, the coating thickness should be checked to ensure that it meets the specified requirements. Coatings that are too thin or too thick can affect the durability and performance of the product.
- Chemical composition: analyze the chemical composition of aluminum to ensure it meets the required standards. This includes checking for impurities or other elements that could affect product quality.
- Packaging and Labeling: Ensure that rolls are properly packaged and labeled for shipping and storage. Packaging should be strong and designed to protect the coil during transport.
- Manufacturing Process: The manufacturing process is inspected to ensure it meets the required standards and that all equipment is properly maintained and functioning.
An effective inspection process will help identify any potential issues with the product and ensure it meets the required quality standards.
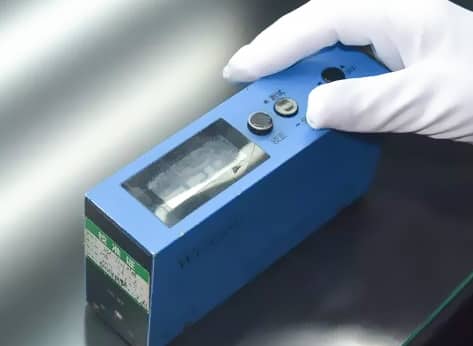

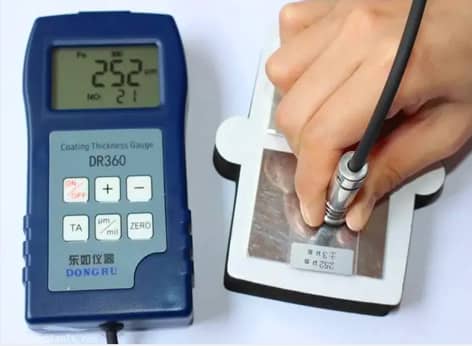

Looking for the ideal aluminum coil for your industry?
We provide custom solutions to all our customers and offer free Aluminum Coil samples that you can take advantage of.
Characteristics of Aluminum Coils
Good temperature resistance.
The melting point of aluminum is 660 degrees, and the general temperature does not reach its melting point.
Rigid joint, extremely high strength of the board:
Rigid and tough combination, free to cut, slit, arc, balance,drilling, joint fixation, and edge compression molding.
Corrosion-resistant:
Aluminum has excellent corrosion resistance, making it suit-able for use in harsh environments.
Easily Machined and Cast:
Aluminum coil is more malleable and easier to pour into molds because it melts faster than steel.
Lightweight and strong:
Aluminum is a lightweight but strong metal, making it ideal for use in various applications.
Ductile.
Aluminum can be easily formed into different shapes without cracking or breaking.
Good conductivity:
Aluminum has good electrical and thermal conductivity
Environmental protection:
Active chemical molecules are stable and easy to recycle,meeting environmental requirements.
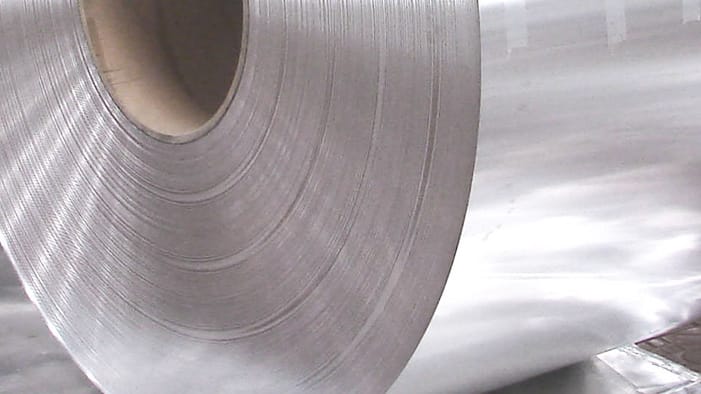
Advantages of Aluminum Coils
- Energy-efficient: Aluminum coils are commonly used in HVAC systems due to their energy efficiency.
- Cost-effective: Aluminum is a relatively low-cost material compared to other metals such as copper or stainless steel.
- Recyclable: Aluminum is 100% recyclable and can be reused indefinitely without losing its properties.
- Versatile: Aluminum coils can be used in various applications, including construction, transportation, packaging, and electronics.
Aluminum Coils Workshop
It has two cold-rolled and hot-rolled production lines with an annual out put of 250,000 tons, two pickling production lines with an annual output of 600,000 tons, and three cold-rolled sheet production lines with an annual output of 100,000 tons.
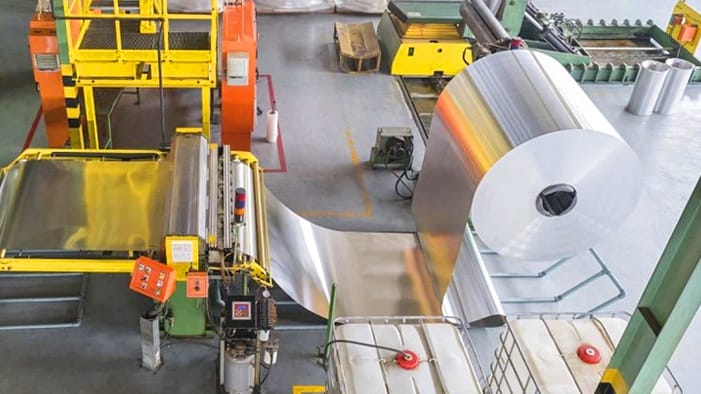
CONTACT US
Call us today for a prompt and competitive quote.